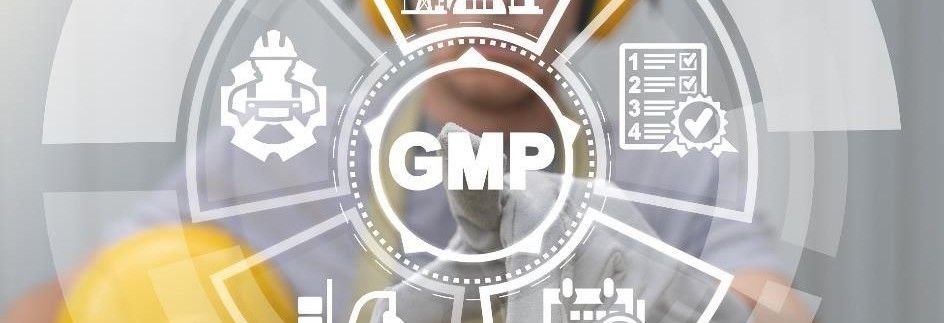

Good Manufacturing Practice: Guidelines for good manufacturing practice
Materials and articles that come into contact with medicinal products, food and feed must not pose a health risk to consumers. Manufacturers of such materials undertake with the Good Manufacturing Practice Directive to optimise their entire process chain for the greatest possible safety. GMP therefore plays a central role in production, both for the substrates used and for printing inks.
Definiton: Good Manufacturing Practice
When quality deviations occur in the composition of medicinal products, cosmetics, food and feed, this usually means negative health consequences for consumers. Good Manufacturing Practice (GMP) therefore offers comprehensive guidelines for quality assurance to avoid such cases.
Since products such as folding boxes and other contact materials can cause quality deviations, they are also included in the GMP rules. The control of production processes and environments as well as the materials used are intended to ensure quality and safety for consumers.
In the case of medicines and other products, deviations in quality can cause serious damage to the health of consumers. The reasons for such quality deviations can lie along the entire production process. To ensure that manufacturers take all necessary measures to exclude such a risk, the guidelines on good manufacturing practice and labelling of medicinal products exist in addition to the legal regulations.
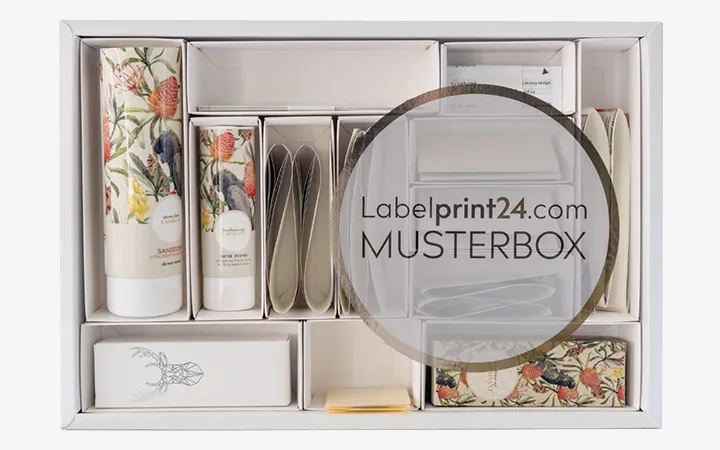
Sample made to measure. Simply order online.
The sample box from Labelprint24 offers you an exclusive selection of products, printed and finished in our company design. We will refund the full purchase price of the sample box in the form of a voucher if you decide to order from Labelprint24. The voucher is of course valid for all products in our webshop.
In this box you will find samples of labels, folding boxes, laminate tubes and package inserts.
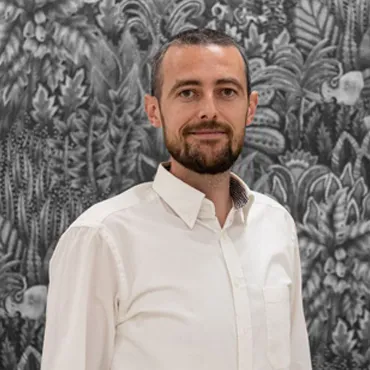
Product consultant Folding Boxes
Whether it’s a simple box or a folding carton with an inlay – I’m your advisor for carton types, base designs, and finishing options. From cosmetics to food and technology, I’ll help you find the perfect folding carton for your industry.
"Just a carton? Folding boxes are incredibly versatile!"
I will be happy to help you personally.
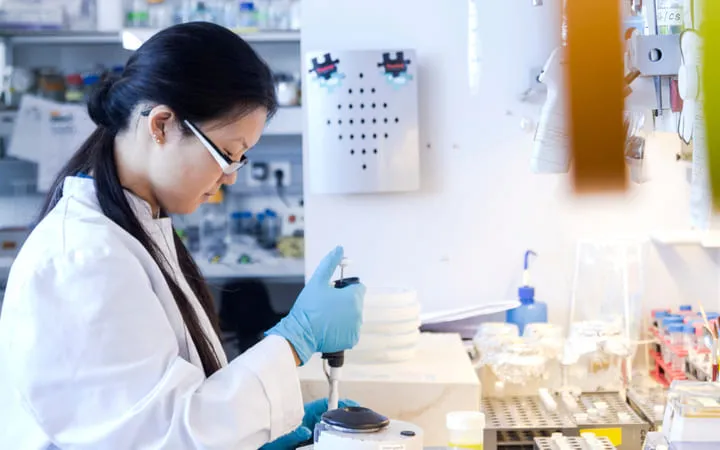
How did the GMP regulations come into being?
In 1968, the World Health Organisation (WHO) published the first guidelines for good guidelines for good manufacturing practice. The reason for the development of the GMP guidelines were recurring cases in which medicinal products did not bring about any improvement in health, but instead caused damage to health and even death. The EU GMP guidelines have been in force in Europe since 2006. They are divided into three areas:
- Part I contains basic requirements that must be met in the manufacture of medicinal products.
- Part II sets out the requirements for good manufacturing practice for active pharmaceutical ingredients.
- Part III additionally lists the necessary documents that are relevant for GMP (for example, quality risk management or the pharmaceutical quality assurance system).
Is there an international GMP guideline?
Since good Manufacturing Practice is incorporated into national legislation, it is handled with corresponding differences. In Germany for example, GMP is a part of the German Ordinance on the Manufacture of Medicinal Product and active substances. Whereas in the USA, the guidelines of current good manufacturing practice apply (cGMP).
Apart from this, there are other international standards that deal with GMP are concerned. For example, for primary packaging materials for pharmaceuticals, ISO 15378 (which in turn refers to ISO 9001) and for cosmetics, ISO 22716.
In addition, various industries are developing special GMP guidelines with more specialised specifications for manufacturing practice, such as the European Carton Makers Association (ECMA) for the European folding carton manufacturers or the European Printing Ink Association (EuP) or the European Printing Ink Association (EuPIA) for printing ink production.
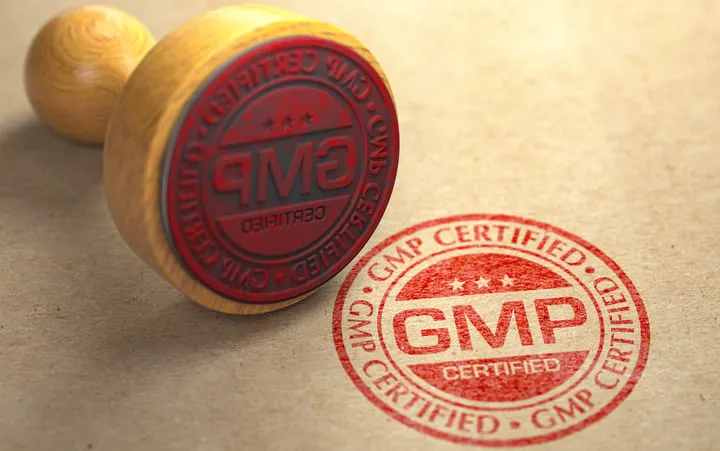
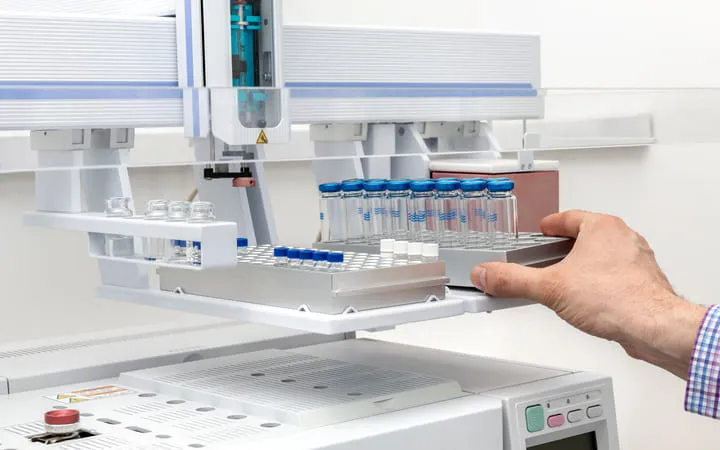
What areas of application does GMP cover?
The GMP guidelines alone do not constitute a quality assurance system. However, they do provide the instruments for a comprehensive quality assurance management. This covers different areas of application, from personnel to premises and hygiene to testing and documentation:
- The staff must be available in sufficient numbers and have the necessary training. According to GMP, this also includes regular further education and training as well as clearly defined responsibilities.
- The premises must be suitable for the respective purpose (production, testing and storage). An appropriate size, sufficient access and adequate cleaning must be proven (in the form of a qualification).
- The same applies to the equipment (i.e. devices and the like), the proper functioning of which must be ensured for the entire duration of use. Evidence of this must also be provided within the framework of GMP.
- Hygiene covers various areas, from the behaviour of the staff to the wearing of protective clothing to regular cleaning, disinfection and waste disposal. Hygiene and safety officers are responsible for compliance with hygiene requirements.
- The documentation should be standardised and comprehensible and suitable for the respective company areas (production, cleaning, etc.). According to GMP specifications, the documents must guarantee the control of changes and deviations.
- The validation of processes and methods should prove that they are carried out according to plan, within set criteria and in a reproducible manner and that they deliver a product that meets the given specifications.
- Change management (change control) must be able to distinguish precisely between planned and unplanned changes, as well as critical (if product quality is affected, for example) and non-critical changes. The same applies to deviation control.
- According to GMP, companies must also ensure appropriate risk management and regularly conduct internal audits.
Why is GMP important for the packaging and printing industry?
The keyword in this context is: migration risk. If packaging materials or printing inks come into contact with food, it must be ensured within the process chain that the quality of the packaged products is not impaired. According to GMP requirements, plastic, paper, cardboard or rubber must not cause any health hazards for consumers.
Safety for food packaging
The guide from the industry organisation ECMA not only addresses all the core areas of GMP, but also provides guidance on the use of inks and varnishes.
They are critical when it comes to food safety, more so as the inks and varnishes are used in various ways for paper and board packaging.
Manufacturers must take details into account, for example when using UV printing inks. This is because these inks react with some paper or board substrates when they are cured by UV irradiation.
The resulting vapours can cause packaged food to spoil, which of course does not comply with GMP requirements.
Under certain circumstances, special low-migration UV coatings may be used. Paper and board are sometimes quite sensitive substrates. They absorb volatile materials from the ambient air, as well as vapours or liquids. This is called migration.
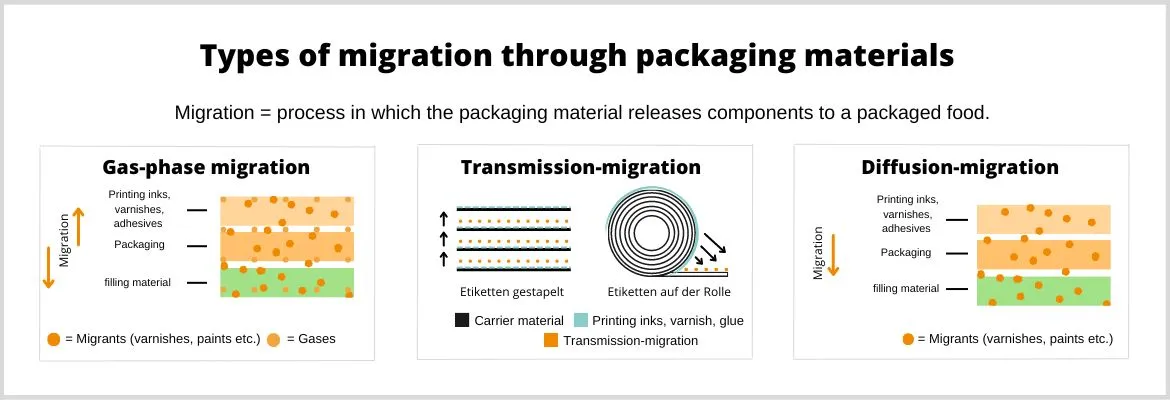
Conclusion
To produce safe packaging within the framework of GMP, all work areas must be designed in accordance with the specifications. The selection of materials and printing inks for the respective products play just as important a role as hygienic production and the avoidance of contamination during all supply routes. A complete documentation serves as a comprehensive proof of quality of a GMP.
At Labelprint24, we are aware of our responsibility towards our customers and the end consumers. That is why we work completely in accordance with GMP requirements in our process chains and thus ensure the safety of the packaging, the packaged goods and the people who come into contact with them at all levels.