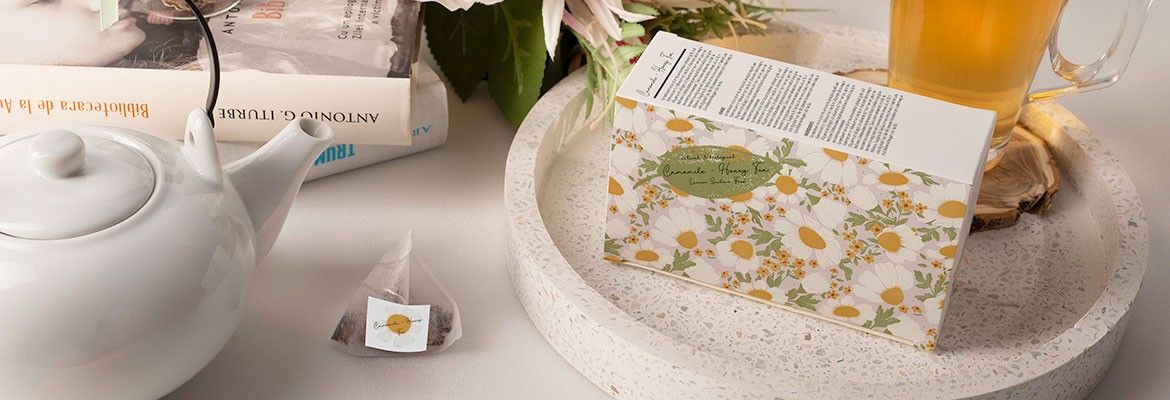

Closure types for folding boxes at a glance
Folding boxes are among the most popular packaging for products of all kinds, because they are delivered folded and thus save a lot of space. When folded, however, the packaging must withstand high demands: It should be stable, securely closed and yet easy to open. For these reasons, there are numerous types of closure for a box made of folding cardboard.
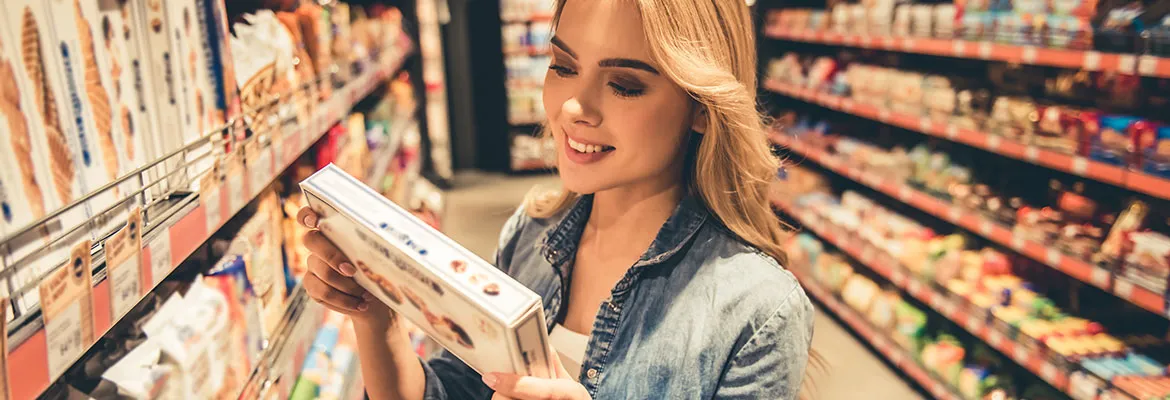
What is a folding box?
Definition: Folding boxes
A folding box or folding carton is a foldable box that is delivered flat to save space. It is formed into its final shape by erecting, folding and in some cases gluing. Usually, folding boxes are made of cardboard, solid board or corrugated board. Their sizes, shapes and colours are variable. Depending on the type, size and weight of the product to be packaged, there are also different types of closure for the box.
How are folding boxes constructed?
All folding boxes have a so-called box body, which is also called a frame. Depending on the model, this is connected with base and lid flaps or with an insertable base and lid. In most designs, the lid closes towards the front in a similar way to a chest. Another important component of many folding boxes is the dust flap. It prevents the penetration of dust particles and other foreign bodies. In the case of lids with tuck-in flaps, it also ensures that the tuck-in flap is correctly locked in place. The dust flap also acts as a counter-pressure that prevents the lid from breaking into the folding box.
The most important types of box closure
Flap gluing
Flap gluing is the most common type of closure for a box. In this process, flaps on the box that are specially designed for gluing are joined with liquid glue. This is applied with a glue wheel or with the help of nozzles. In most cases it is a dispersion adhesive, which is mostly waterproof when dry. The most important advantage of flap gluing is the fast, clean processing.
Tape gluing
Tape gluing is also one of the most common types of closure for a box made of folding material. It is also known as strip gluing or taping. With this method, the blank of the box is fed to the sealing station in a folded state, while the adhesive strip runs from a roll. Wet adhesive strips are moistened, hot melt adhesive strips are heated. The adhesive tapes are then cut and glued over both outer edges with the help of pressure. As the cut edges have to butt together, a flap is not used.
Wire staple stitching
For wire stapling, the carton blank is fed from the folding station to the closing station. If it is directly under the stapling head, a stapling process is triggered. Here, the stitching head forms a staple from flat wire that is unwound from a roll. It drives the staple through the cardboard layers that are to be joined and bends it on the back. With a flat load, wire stapling has a similar stability to tape bonding. However, if a non-area load is applied to stapled factory edges, the staples can yield in a similar way to a zip fastener. In addition, the internal stapled edges can interfere with the packaging of certain goods. In such cases, it is advisable to choose tape or flap gluing instead of stapling.
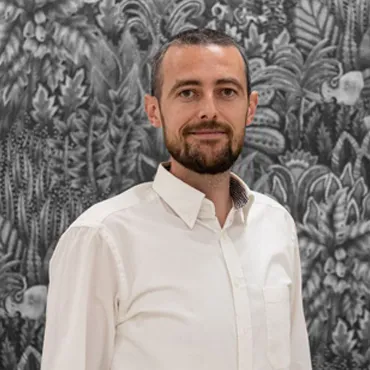
Product consultant Folding Boxes
Whether it’s a simple box or a folding carton with an inlay – I’m your advisor for carton types, base designs, and finishing options. From cosmetics to food and technology, I’ll help you find the perfect folding carton for your industry.
"Just a carton? Folding boxes are incredibly versatile!"
I will be happy to help you personally.
Base and lid moulds for folding boxes

Boxes with tuck-in flaps
Folding boxes with tuck-in flaps are particularly easy to assemble and are therefore the most common form of closure. Both the bottom and the top can be closed stably with the help of two dust flaps and a tuck-in flap. The tuck flap is a protruding part of the folding box that is pushed into the inside or outside of the box. The flap can extend over the entire width of the box or be much smaller. A combination of several tuck-in flaps is also possible. Insert flaps are one of the most popular types of closure for a carton as primary packaging in which, for example, medicines are to be packed. They are also suitable for cosmetics packaging.
There are several types of closure for a box with tuck-in flap:
- Locking flap: The tuck-in flap has a slot on each side of the front edge. They lock on the side dust flaps to ensure a stable and secure closure.
- Friction closure: Insert flaps with friction closure do not have a locking slot, as the focus is on the uniform and elegant appearance of the lid and edge. Since the lack of a locking slot affects stability, the friction lock is only suitable for the top of the box.
- Closing tongue: The closing tongue is an additional, smaller flap that is opposite the large tuck-in flap. It is inserted into a slot between the top flap and the tuck-in flap, thus ensuring greater protection for the contents of the box.
- Side flaps: This form of folding box has two flaps, one of which is inserted at the top inside of the box walls and the other subsequently from front to back. The tuck flap and the side flap combine to ensure that the folding box is firmly closed from top to bottom as well as from front to back.
Folding boxes with tuck-in flaps have numerous advantages and are also used as secondary packaging. For example, they can be closed very easily with just one flick of the wrist. In addition, it is possible to open and reseal the boxes several times. Even after frequent use, the closure does not wear out or lose stability. However, an additional closure with adhesive tape is recommended for transport. If there is no closing tongue, the box may open in the event of a jerky movement.
Insertable shelf
A push-in bottom consists of four flaps, each attached to one side of the bottom. If you straighten up the box, you can fold the bottom flaps inwards. Since they hook into each other, there is no need to glue them together. The closure can be opened again later, turning the tuck bottom into reusable packaging. Folding cartons with a tuck-in bottom is one of the best types of closure for a carton that is intended to carry medium to heavy weights. The weight of the products has a strengthening rather than destabilising effect, as the flaps are folded inwards and the weight acting on them provides more stability.
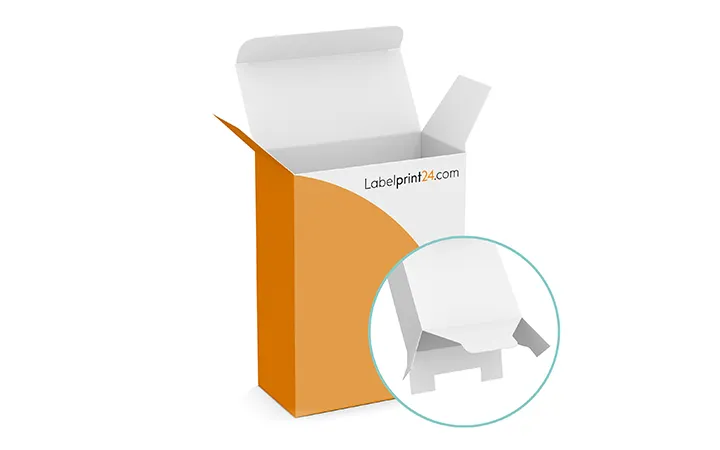
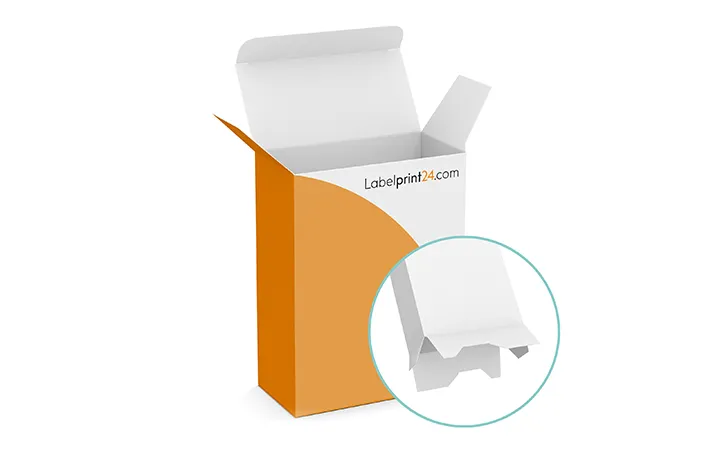
Automatic bottom
The folded bottom has already been glued in the manufacturing process and can be erected with just one movement. To do this, simply push the flat carton together on both sides. Compared to classic folding boxes, which have to be glued first, folding boxes with automatic bottom offer enormous savings in time and material. The automatic bottom has a very high load-bearing capacity and is considered one of the most stable closure types for box bottoms. The boxes are very suitable for machine filling and for transporting goods with a high tare weight. The only disadvantage is that automatic bottoms are difficult to fold back to the flat state after they have been erected once.
Special closure types for the box
Hanging boxes
Suspension boxes have a sturdy additional flap with a so-called Euro hole, a punched-out slot in the lid. The Euro hole makes hanging boxes one of the most suitable types of closure for a box to be displayed at retail.
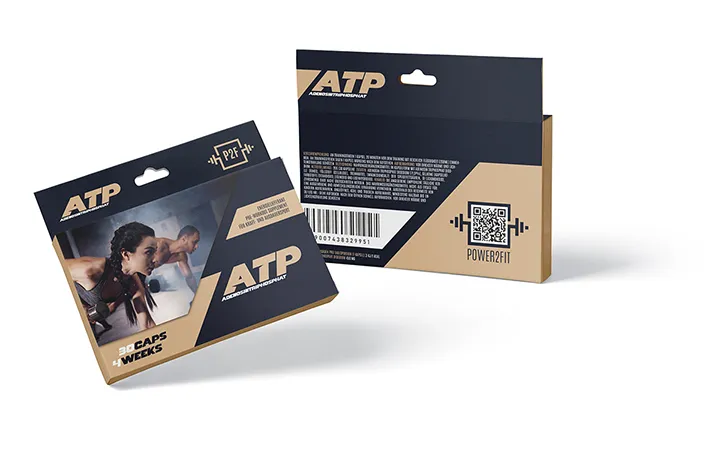
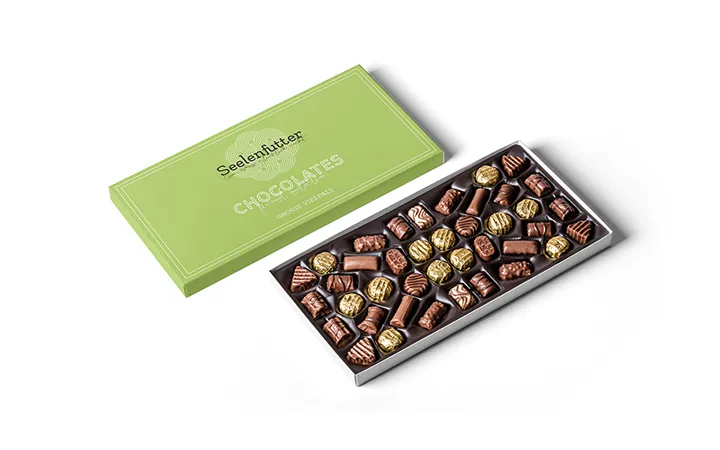
Slip lid boxes
Slip lid boxes are made of two parts and consist of a loose lid that is slipped over the bottom of the printed packaging from above. In most cases the boxes are made of solid board, but there are also products made of corrugated board. In some cases, the slip lid boxes are height-adjustable, which makes the slip lid one of the best types of closure for a box whose packaged goods vary. In addition, the boxes usually only need to be erected and not glued, which saves a lot of time.
Carry handle boxes
The carry handle box is a folding box that does not require gluing and has been provided with a handle on the top. Its double material thickness ensures greater stability. Another advantage is that the handle box can be resealed.
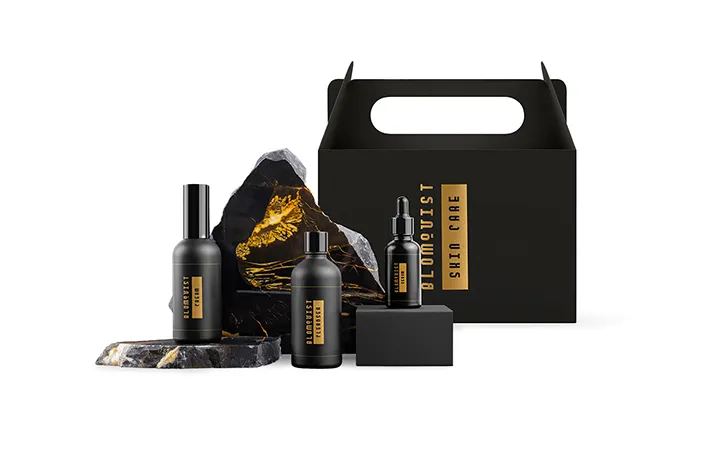
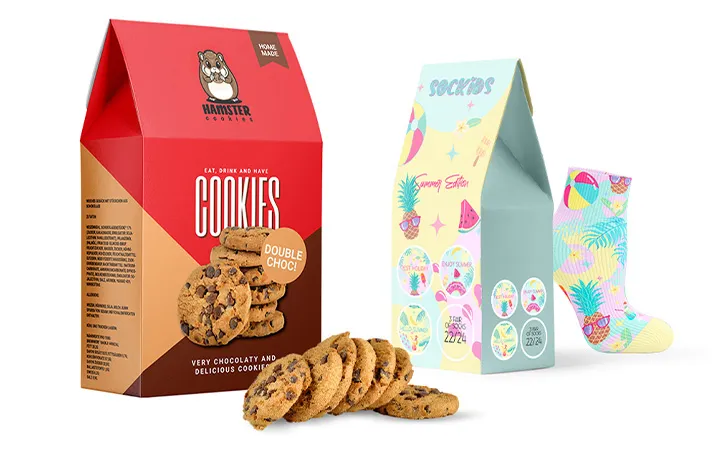
Pouch boxes
The tapered closure of the sachet box is considered one of the highest quality closure types for a box. These cardboard packages are often used for tea, herbs or spices.
Pillow boxes
Although they do not have a tuck-in closure, pillow boxes are also considered folding boxes. The special stability of this closure comes from the tension built up by the convex shape.
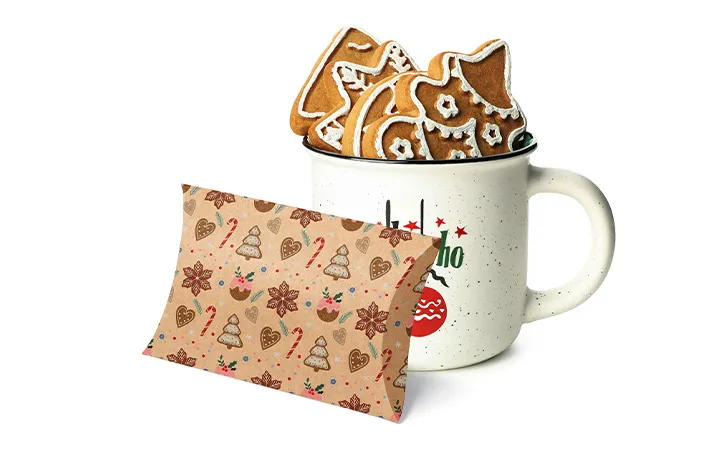