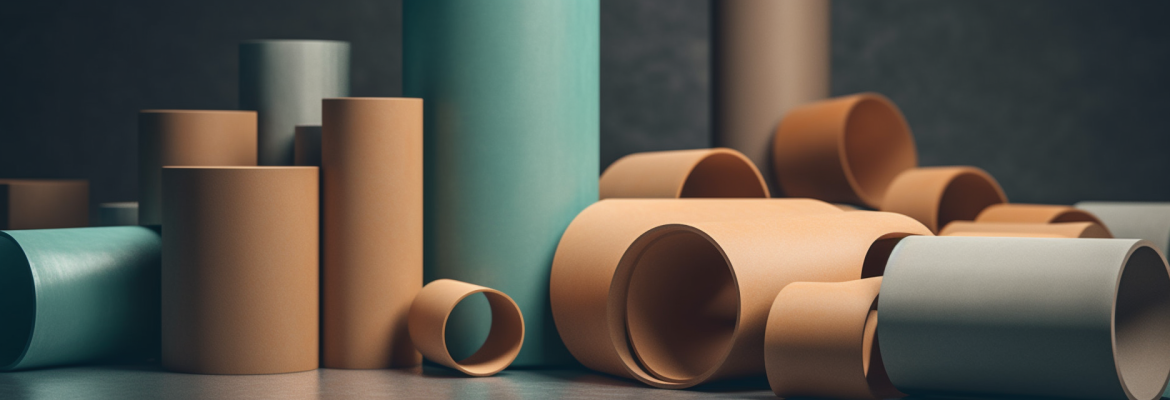

Roll cores for labels
It's hard to imagine roll labels without a roll core - offered in a wide range of core diameters, our round label carriers are suitable for a variety of labelling options. From manual labelling to fully automated label dispensers - fast labelling would simply be impossible without the practical cores.
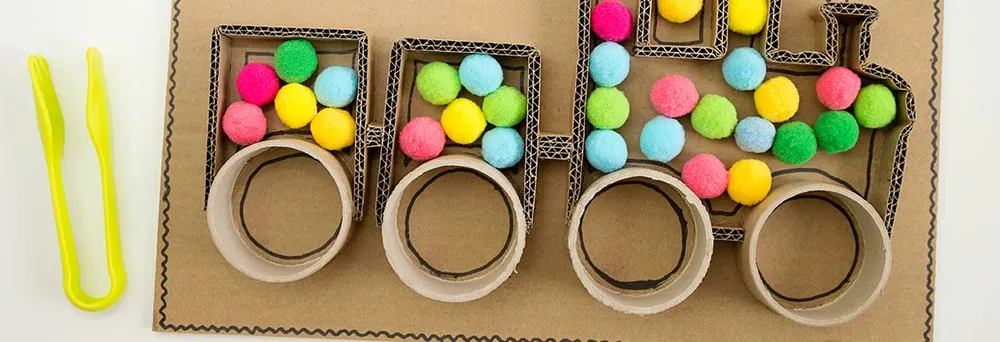
Definition of roll core
Roll cores are cardboard or plastic cores onto which the label web - consisting of the backing material and the labels arranged on it - is wound. For both production and application reasons, roll labels are typically wound onto cores in a specified winding direction - here, the roll cores ensure stability and safe transport while enabling hassle-free processing down the line. Roll cores can also be known as hard paper cores, cardboard rings, or winding cores.
Core diameter
When machine processing labels, the core diameter depends on the maximum outer roll diameter and the maximum roll width of the label dispenser or label printer used. Our roll cores range from 12.7 mm to 101.6 mm, while the most common core diameters are 26 mm, 40 mm, 50 mm and 76 mm. In addition to machines with inflexible core holders, we also offer dispensers with adjustable core holders: these are suitable for roll cores from 25-101mm and can be used as label unwinders and rewinders.
Choosing the right roller core
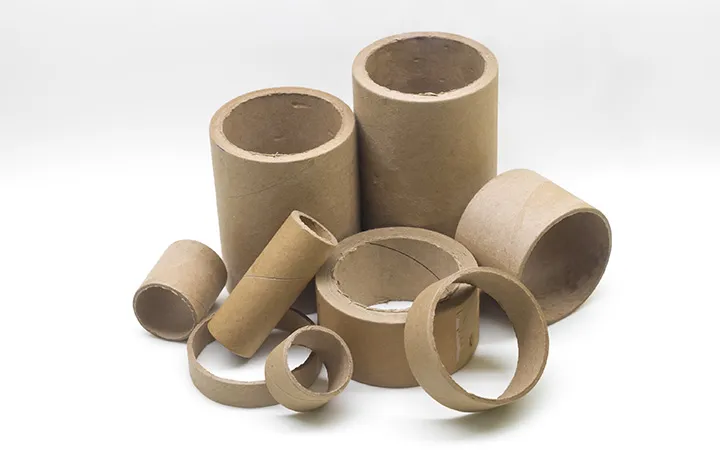
Choosing the right roll core depends on several factors. Basically, a small roll diameter means that there is room for many labels per roll. However, the smaller the roll core, the more the labels can curl during rewinding, which can lead to difficulties during automatic dispensing.
When labelling by hand, you want a relatively small yet functional diameter such as 30 mm; for labels with a height of over 75 mm, you want a larger core so that the labels do not bend too much when they are rolled up.
For semi-automatic or fully automatic label dispensers or label printer dispensers, the roll core must match the specifications of the devices. Desktop label printers usually require a core diameter of 26mm, while industrial label printers require either 40 mm or 76 mm.
Structure and functions of the roller core
Roll cores are usually made from environmentally friendly cardboard or paperboard. Plastic cores are used less frequently and are more so required for special tasks such as cleanroom applications. In addition to winding labels, the cores are also used for other materials such as films, adhesive tapes, etc. The cores are also used to prevent transport damage, to help cover small parts or as spacers.
The roll cores can have a wall thickness of up to 12 mm and consist of spirally wound cardboard webs. The cover web can be wound ‘butt to butt’ or ‘overlapped’. In addition to the standard version in natural brown, the inner and outer webs can be white or coloured and provided with an individual spiral print.
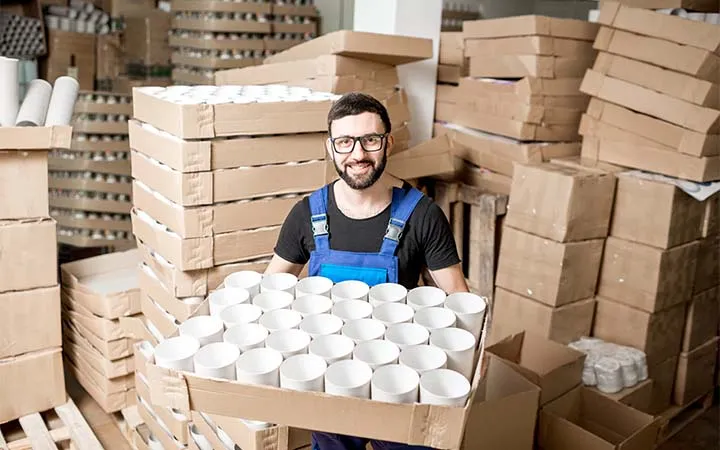
Quality product core
Roll cores are not only required for printing labels, but also for winding paper, photo paper or film. The dust-free winding core required here is characterised by its high dimensional stability and special surface treatment. Additionally, it is dried according to strict procedures and therefore has a balanced moisture content. The roll cores must fulfil numerous quality criteria to ensure that there are no failures when the stickers or booklet labels are dispensed. These include:
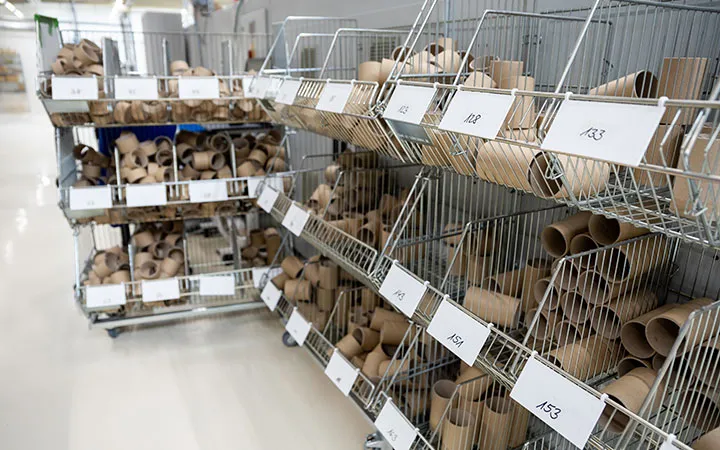
- Gluing
- Straightness
- Compressive strength
- Moisture content
- Dimensional stability (shrinkage)
- Impression resistance
- Smoothness/roughness of the outer surface
- E-modulus (vibrations at high revolutions)
- Radial breaking strength (compression of the entire roller surface)
- Dynamic load - pressure on the roller core due to a combination of weight and (un)winding speed
Conclusion
Space-saving storage, secure transport and fast label dispensing - three goals our range of roll cores help realise. These versatile cardboard cores transport a large number of labels and increase the efficiency of the production process, especially in combination with automated label dispensers.