LIKE A SECOND SKIN MADE OF PLASTIC - LAMINATING
Printed matter with high-quality glossy surfaces or elegant matte effects exudes a very special fascination. Every degree of gloss has an individual, emotional effect that is deliberately used to enhance the quality of a print product. To achieve this effect, print shops and packaging manufacturers use a special type of finishing, lamination. But laminations can change a printed product not only visually, but also haptically. A laminated surface feels cool or pleasantly soft, depending on which laminate was used.
Almost all Labelprint24 products can be customized with lamination. These include labels, booklets, sandwich labels and laminate tubes. Even our folding boxes are often ordered with this "second skin" of plastic. And for good reason.
FOLDING BOXES WITH "LOOK AND FEEL" EFFECT
An emotionally appealing and sales-promoting design is particularly important for folding cartons. High-quality materials and eye-catching finishes further enhance the surface of folding cartons. Haptics also play an important role and are specifically influenced. Of course, the valuable, highly refined surface of the boxes must also be protected from external influences and UV-induced aging. The optimum solution for this is a laminate.
When folding cartons are laminated, the folding carton board is enclosed on both sides by an ultra-thin laminate film made of PET, OPP or bio-films. The laminate serves to protect the custom-made cartons from mechanical influences such as scratches, moisture and sunlight. Depending on which film is used for lamination, the base material is given either a brilliant gloss, a matte or soft-touch surface.
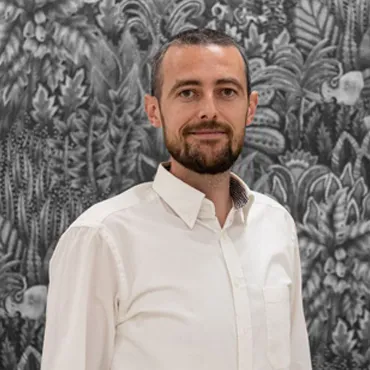
Ronan Joncour
Product consultant Folding Boxes
Whether it’s a simple box or a folding carton with an inlay – I’m your advisor for carton types, base designs, and finishing options. From cosmetics to food and technology, I’ll help you find the perfect folding carton for your industry.
"Just a carton? Folding boxes are incredibly versatile!"
I will be happy to help you personally.
WHAT IS MEANT BY LAMINATING?
During lamination, an ultra-thin plastic film, for example made of polyester, is applied to one or both sides of the packaging material. Various films with different surfaces are available for this purpose: Matt films, glossy films or soft-touch films.
There are two different processes for this in print finishing. In cold lamination, adhesive-coated films are applied to the packaging materials under pressure. The film immediately adheres cleanly and securely to the surface of label webs or cardboard sheets.
In hot lamination, special protective laminate films are applied to the printed matter under the influence of heat and fused. This requires a laminator with rollers. The rollers are heated to a temperature of about 90 degrees. The heat causes the film to melt and bond firmly to the print substrate without destroying it. This laminate composite must then be dried and cut to size. This process is also used to make ID cards, menus, table mats or similar printed materials permanently durable.
PROTECTION AND REFINEMENT IN ONE
However, the laminating film not only protects against loss of quality, but also enhances the surface, both visually and haptically. Folding cartons and labels with a laminated surface look more sophisticated and of higher quality than other printed matter. High-gloss film, for example, achieves a much higher gloss effect than a gloss coating.
When laminating, the visual effect depends on whether glossy, matte or soft-touch films are used. Glossy films enhance the effect of the printing inks due to their glossy surface. Due to their roughened structure, matte laminate films reduce light reflections on the surface and thus make the print motif more pleasant to read. The color perception is somewhat softened; the typical noble, matte surface impression is created.
The soft-touch effect is used for a special feel. Depending on the laminate, it feels velvety, rubbery or pleasantly soft. Almost like a second skin. Finishing with soft-touch lamination opens up completely new dimensions and a very emotional approach to the product. As a rule, soft-touch foils are transparent. Each type of lamination ensures durability and stands for a high value of packaging and content.
Discover also our range of labels.